Local News
TTC board hears plan to address maintenance issues after 2024 subway system hydraulic oil spills
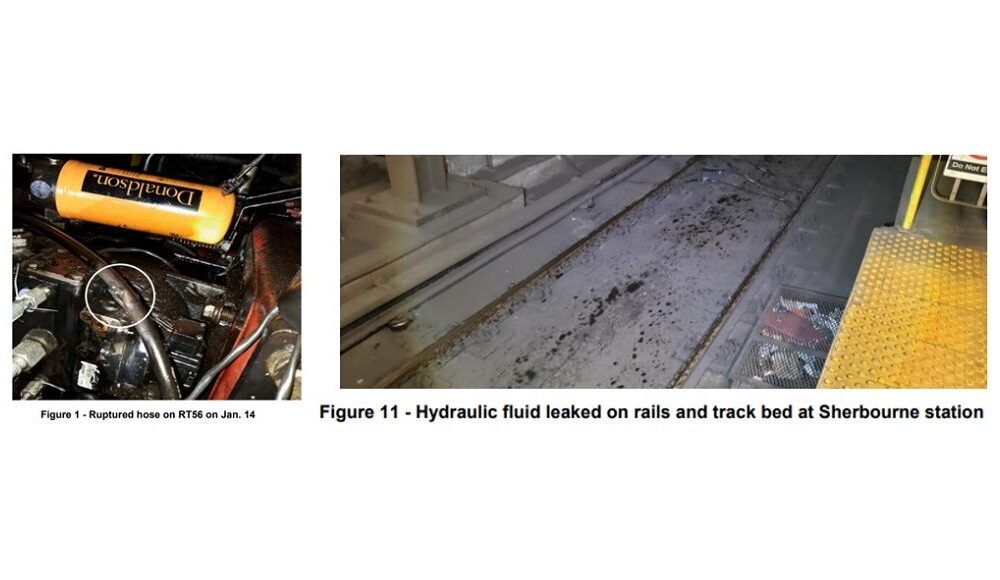
After a significant hydraulic oil leak earlier in 2024 that forced a half-day closure of TTC Line 2 and the revelation of several other smaller incidents, the transit agency’s board has received an update on a plan to address associated maintenance issues.
“Sometimes people ask as a board member at the TTC what keeps you up at night, reports like these do. I think they’re very serious,” Toronto Coun. Stephen Holyday said during Tuesday’s meeting.
“I’m glad that the consequences of hydraulic fuel leaks on tracks don’t have a sad and tragic ending, but they’re serious enough to make me think and pause and ask a lot of questions.
“I hope we do better. I expect that we do better. I know we can do better.”
Holyday was one of several board members who questioned TTC staff and independent experts brought in to examine issues related to maintenance vehicles and procedures.
It was on May 13 when Line 2 was closed between St. George and Broadview stations for nearly 12 hours after a work car hose leaked oil on the track between Bloor-Yonge and Castle Frank stations. Officials at the time said it created “slippery track conditions” that required manual track cleaning. The closure disrupted the commutes of tens of thousands of riders.
Advocates once again raised concerns and questions about TTC maintenance and funding, pointing to issues like a cracked rail switch in March that disrupted trains and ongoing issues with restricted speed zones. The aging Line 3 Scarborough RT was forced to close months earlier than hoped for in 2023 after a train derailed and that was blamed on loose track bolts.
Three days later, it was revealed seven hydraulic leaks happened earlier in the year. An eighth one occurred at the end of May. There were only four between 2019 and 2023. The incidents were less severe than the May 13 issue. However, then-CEO Rick Leary ordered a forensic review of the situation by two engineering consulting companies, Hatch and Acuren, as well as a peer review by the American Public Transit Association (APTA).
On Tuesday, the board received a report containing the results of that review.
“Hatch’s investigation established there is no evidence to support the notion that the eight incidents were caused by nefarious actions, despite the unusually high number of occurrences over a short period of time,” the Hatch report said.
It said the incidents appeared “to be isolated failures” caused by three common factors: A lack of detailed information in the TTC’s maintenance reporting system, maintenance intervals not sufficient or known, and “inadequate configuration control” and “limited availability of reference documentation.”
Acuren looked at the damaged hydraulic hose from May 13 and found abrasive wear was likely the cause of damage, and wear marks were found on wires.
“Over years of service, the motion of the hose against the ring caused wear and visible abrasions on the hose. The continued abrasion of the hose exposed the wire mesh which created a sharp edge on the ring and eventually caused the hose to fail, enabling hydraulic fluid to leak from the hose,” the Hatch report said.
The APTA review suggested beefing up communication protocols and resources and “aligning” the same incident management processes buses, streetcars and subway trains have with vehicles not used for passengers. It also found “common technical root causes” but no evidence of intentional damage by sabotage.
“Both reports identified common root causes, and while they found that the TTC’s practices are typical of the industry, they recommend implementing a more robust preventative maintenance program of procedures, training, and quality control modelled after what the TTC has in place for revenue service vehicles,” TTC staff wrote in response.
“The TTC recognizes that hydraulic leaks can significantly impact the customer and employee experience.”
The reviews from Hatch and APTA contained 27 recommendations and TTC managers said they’ve agreed to implement all. Many are complete or in progress while some stretch out as far as 2029.
Recommendations dealt with things like overhauling various maintenance procedures, standards and guidelines, boosting quality assurance resources, increasing inspection regimens, better updating and completing inventory and maintenance notes in the TTC’s electronic systems, conducting more training and testing of emergency scenarios, and considering additional public communications resources.
There are 75 subway infrastructure maintenance work cars. The TTC set aside $34 million to overhaul aging work vehicles while $63.4 million has been earmarked to buy new equipment. Staff noted the fleet of work cars is “highly varied and each car’s configuration and operating environment are largely unique.”
Interim TTC CEO Greg Percy, who joined the transit agency in early September on an eight-month contract after Leary resigned in August, said he and senior managers are looking at ways to “step up the robustness” of maintenance and inspection procedures.
“I don’t think this is an investment issue. I think it’s a process issue. We need to have robust process that needs to be closely followed,” he told the board.
“Typically in my experience, I would look to the supervisors who should own the process as opposed to the front line who actually do it. You’ve got to have quality control.”
He said he wants to “turn a negative into a positive” and apply lessons learned to other mechanical components similar to the ones cited as having issues.
TTC internal auditors are also scheduled to follow-up on the implementation of new quality assurance processes to make sure those meet what was recommended in the reviews.